本文已被:浏览 747次 下载 1020次 |
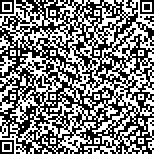 码上扫一扫! |
|
航天发动机大直径不锈钢整体弯头
内高压成形缺陷控制研究 |
李元鹏1,2, 黄显球1,2, 周兴梁1,2, 刘 伟1,2, 韩晓飞3, 刘学峰3
|
1. 哈尔滨工业大学材料科学与工程学院,哈尔滨 150001;2. 哈尔滨工业大学金属精密热加工国家级重点实验室,哈尔滨 150001;3. 西安航天发动机有限公司,西安 710100
|
|
摘要: |
大直径弯头是航天发动机燃料传输系统的关键构件,传统工艺采用冲压半管再拼焊成形方法难以满足高空间利用率和高可靠传输的需求。本文提出一种整体弯头内高压成形方法,利用轴向进料调整管料轴向应变状态,降低内外侧壁轴向应变,避免破裂缺陷的同时提高整体弯头尺寸极限与成形性,理论计算内外侧壁理想进料量分别为21 mm和24 mm。实验中通过改善润滑条件促进了轴向进料,避免因管料与模具间摩擦力过大时无法有效进料导致的破裂缺陷。预弯管件预成形时存在变形强化,通过退火热处理降低硬度,消除残余应力,提升塑性变形能力。成形的1Cr18Ni9Ti不锈钢整体弯头相对弯曲半径0.75、径厚比67,直径200 mm,最大减薄率约为31%。 |
关键词: 整体弯头 小相对弯曲半径 薄壁 内高压成形 |
基金项目:国家自然科学基金资助项目(523***19) |
|
Research on Hydroforming Defect Control of Large Diameter Stainless Steel Integral Elbow of Aerospace Engine |
Li Yuanpeng1,2, Huang Xianqiu1,2, Zhou Xingliang1,2, Liu Wei1,2, Han Xiaofei3, Liu Xuefeng3
|
1.(1. School of Material Science and Engineering, Harbin Institute of Technology , Harbin 150001;2. National Key Laboratory for Precision Hot Processing of Metals, Harbin Institute of Technology, Harbin 150001;3. Xi’an Aerospace Engine Co., Ltd., Xi’an 710100
|
Abstract: |
The large-diameter elbow is the key component of the fuel transfer system of space engine. The traditional method of stamping half-pipe reforming is difficult to meet the demand of high space utilization and high reliable transmission. In this paper, a hydroforming method of integral elbow is proposed, which uses axial feeding to adjust the axial strain state of pipe material, reduce the axial strain of inner and outer side walls, avoid the fracture defect, and improve the size limit and formability of the integral elbow. The theoretical calculation of the ideal feed amount of inner and outer side walls are 21 mm and 24 mm respectively. In the experiment, the axial feeding was promoted by improving the lubrication conditions, and the rupture defect caused by the excessive friction between the pipe material and the mold could not be effectively fed was avoided. There was deformation strengthening in the preforming of the prebending pipe, and the hardness was reduced by annealing heat treatment, the residual stress was eliminated, and the plastic deformation ability was improved. The formed 1Cr18Ni9Ti stainless steel integral elbow had a relative bending radius of 0.75, a diameter to thickness ratio of 67, a diameter of 200 mm, and a maximum thinning rate of about 31%. |
Key words: integral elbow small bend radius thin-wall hydroforming |