本文已被:浏览 19次 下载 25次 |
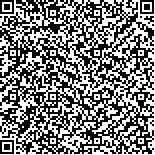 码上扫一扫! |
|
基于CF/PEEK带材的空间桁架结构在轨连续制造工艺设计与验证 |
颜家勇1, 田帅2,3, 李鹏*2,3, 耿超2,3, 潘金启1, 孙雪君1, 张利新1, 赵志虎1
|
1. 北京卫星制造厂有限公司,北京 100094;2. 燕山大学机械工程学院,秦皇岛 066004;3. 河北省装备轻量化设计与制造创新中心,秦皇岛 066004
|
|
摘要: |
本文聚焦大型空间桁架结构在轨制造技术,以连续碳纤维增强聚醚醚酮(CF/PEEK)带材为原材料,旨在实现高效在轨连续制造。研究对比了连接单元跟随斜杆双旋向缠绕、仅斜杆双旋向缠绕、仅纵梁单向旋转三种桁架缠绕成形与连接方案,综合考虑斜杆类型、整体尺寸、焊机自由度等因素,选定仅斜杆双向缠绕方式,该方式可保证斜杆多样性和力学性能,且连接不受缠绕单元尺寸和电滑环负载限制。搭建桁架缠绕成形试验平台,采用CF/PEEK单向预浸带开展边长100 mm正三角形、节点间距100 mm的人字形构型桁架结构的成形验证试验,制造出的桁架节点间距均为100 mm,验证了超长桁架连续制造能力。最后,对长度为1.2 m、1.8 m、2.4 m和3.8 m的桁架结构进行120 g配重基频测试,测试结果表明,随着桁架长度的增加,基频从56.29 Hz降低至28.92 Hz,满足使用需求。 |
关键词: CF/PEEK 在轨制造 空间桁架结构 拉挤成形 纤维缠绕 |
基金项目: |
|
Design and Verification of Continuous Manufacturing Process for Space Truss Structure on Orbit Based on CF/PEEK Strip |
Yan Jiayong1, Tian Shuai2,3, Li Peng*2,3, Geng Chao2,3, Pan Jinqi1, Sun Xuejun1, Zhang Lixin1, Zhao Zhihu1
|
1. Beijing Spacecraft Manufacturing Co., Ltd., Beijing 100094;2. Mechanical Engineering College, Yanshan University, Qinhuangdao 066004;3. Hebei Innovation Center for Equipment Lightweight Design and Manufacturing, Qinhuangdao 066004
|
Abstract: |
This paper focused on the on-orbit manufacturing technology for large-scale space truss structures, using continuous carbon fiber-reinforced polyetheretherketone (CF/PEEK) tape as the raw material, with the aim of achieving efficient continuous on-orbit manufacturing. The study compared three truss winding and connection schemes: double helical winding of diagonal members with the connection unit following, double helical winding of diagonal members only, and unidirectional rotation of longitudinal beams only. Considering factors such as the type of diagonal members, overall dimensions, and the degrees of freedom of the welding machine, the scheme of double helical winding of diagonal members only was selected. This method ensured the diversity and mechanical properties of the diagonal members, and the connection was not limited by the size of the winding unit or the load of the electrical slip ring. An experimental platform for truss winding and forming was constructed, and a forming validation test was conducted using CF/PEEK unidirectional prepreg tape to manufacture a truss structure with a rhombic configuration, a side length of 100 mm, and a node spacing of 100 mm. The manufactured truss had a node spacing of 100 mm, which verified that the speed matching parameters were practical and demonstrated the feasibility of the continuous truss manufacturing process. Finally, fundamental frequency tests with a 120 g weight were conducted on the truss with a length of 1.2 m, 1.8 m, 2.4 m, and 3.8 m, respectively. The results showed that the fundamental frequency decreased from 56.29 Hz to 28.92 Hz with the length decreased which meet the requirements. |
Key words: CF/PEEK on-orbit manufacturing space truss structure pultrusion forming fiber winding |